New to Climate Change?
Steel
Steel is a foundational material for modern society. The world makes almost 2 billion tonnes of it a year, an amount that has more than doubled in 20 years as fast-developing countries expand their cities and infrastructure.1
But the huge energy needs of steel mills, and the basic chemistry of steelmaking, mean that all this steel comes with a heavy toll in carbon dioxide (CO2), the most important climate-warming greenhouse gas. The iron and steel sector is, alongside concrete, one of the world’s most climate-polluting heavy industries, accounting for nearly 9% of all humans’ CO2 emissions.2
Steelmaking and climate change
High-quality steel is over 99% iron. The rest is carbon and very trace amounts of other elements like manganese and silicon.
But iron ore, the raw material for steel, is mostly iron and oxygen. The key to making steel, then, is “reduction,” or taking the oxygen out of the ore.
Usually, reduction happens in a blast furnace. Here, iron ore is mixed with a coal-based fuel called “coke” at very high temperatures. The oxygen in the ore combines with the carbon in the coke to make CO2. What’s left is mostly iron with a few percent of carbon. Further refining adds trace elements and lowers the carbon content to just the right level to make strong, shapeable and durable steel.
All this takes a tremendous amount of energy, in particular chemical energy. A large steel plant producing four millions tonnes of steel a year has energy needs equivalent to the output of a nuclear power plant. Most of this energy comes from coal. And because the carbon in the coal is needed for the reduction of iron oxide, the coal can’t simply be switched out for any clean energy source.
Despite these challenges, the steel industry has made great strides in limiting its reliance on coal. Modern steelmaking is incredibly energy-efficient, using 60% less energy per ton of steel than in 1960.3 But these advances have come because steelmakers profit from using recycled steel and minimizing coal use. Altogether, energy and coal amounts to nearly half the cost of steel production from iron ore, and existing plants are already using as little energy as possible to save costs. More fundamental changes to how steel is made will face a harder road.
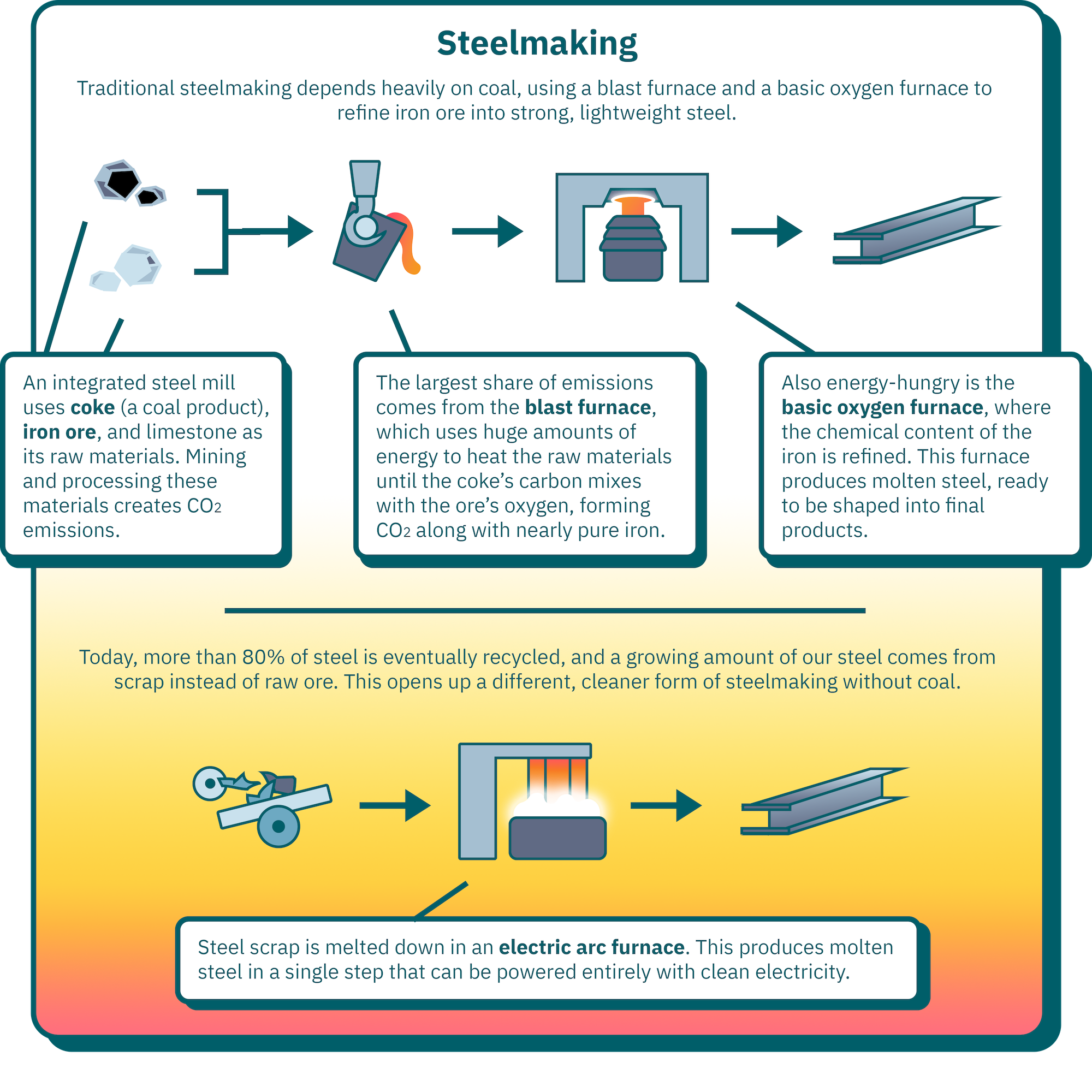
Click here to see information from the infographic above in a table.
Steelmaking Process | Climate Impact |
---|---|
Raw materials | A traditional integrated steel mill uses coke (a coal product), iron ore, and limestone as its raw materials. Mining and processing these materials creates CO2 emissions. |
Blast furnace | The largest share of emissions in steelmaking comes from the blast furnace, which uses huge amounts of energy to heat the raw materials until the coke’s carbon mixes with the ore’s oxygen, forming CO2 along with nearly pure iron. |
Basic oxygen furnace | The basic oxygen furnace, where the chemical content of the iron produced in the blast furnace is refined, is also energy-hungry. This furnace produces molten steel, ready to be shaped into final products. |
Electric Arc Furnace | Today, more than 80% of steel is eventually recycled, and a growing amount of our steel comes from scrap instead of raw ore. This opens up a different, cleaner form of steelmaking without coal. Steel scrap is melted down in an electric arc furnace, which produces molten steel in a single step that can be powered entirely with clean electricity. |
Toward clean steel
Engineers have proposed and even built many alternative approaches to making steel, with the goal of lowering or eliminating CO2 emissions.
The most straightforward is to add carbon capture technology to a standard steel plant. At an added cost, this technology can take the CO2 out of the exhaust from the blast furnace, to be buried underground where it can’t contribute to climate change.
Recycled steel can also help lower emissions. An electric arc furnace, which can be powered with clean electricity, turns steel scrap into fresh steel for reuse. But steel is already recycled at a very high rate: in the U.S., around 70% of steel manufacturing comes from scrap.4 With the world’s growing demand for steel, scrap use cannot be pushed much higher. And recycled steel melted in arc furnaces is often of lower quality: suitable for rebar used in construction, but not for car frames or suspension bridges.
All other routes to clean steel must rethink the basic chemistry of steelmaking. For instance, other fuels than coke could be used in reduction: methane gas (which has lower but not zero emissions), or clean hydrogen, or biofuels. Electrolysis uses no fuel at all, reducing iron oxides with an electric current. It might even be possible to use iron sulfide instead of iron oxides as a raw material, with sulfur byproducts instead of CO2.
Many of these solutions add new challenges to the chemistry of steel production, which demands a delicate balance between iron, carbon and trace elements. And to have truly clean steel, the world will also need cleaner ways of mining iron ore.
But perhaps the biggest challenge is to compete in the remarkably efficient steel market. Modern steelmaking is a marvel of engineering, producing massive amounts of a highly refined product for as little as 20 cents a pound, and doing so quickly enough to fill large orders on schedule. Any clean steel technology will need to be just as fast, cheap and flexible—or will need some form of government taxation or subsidy (like a carbon tax) to help it compete.
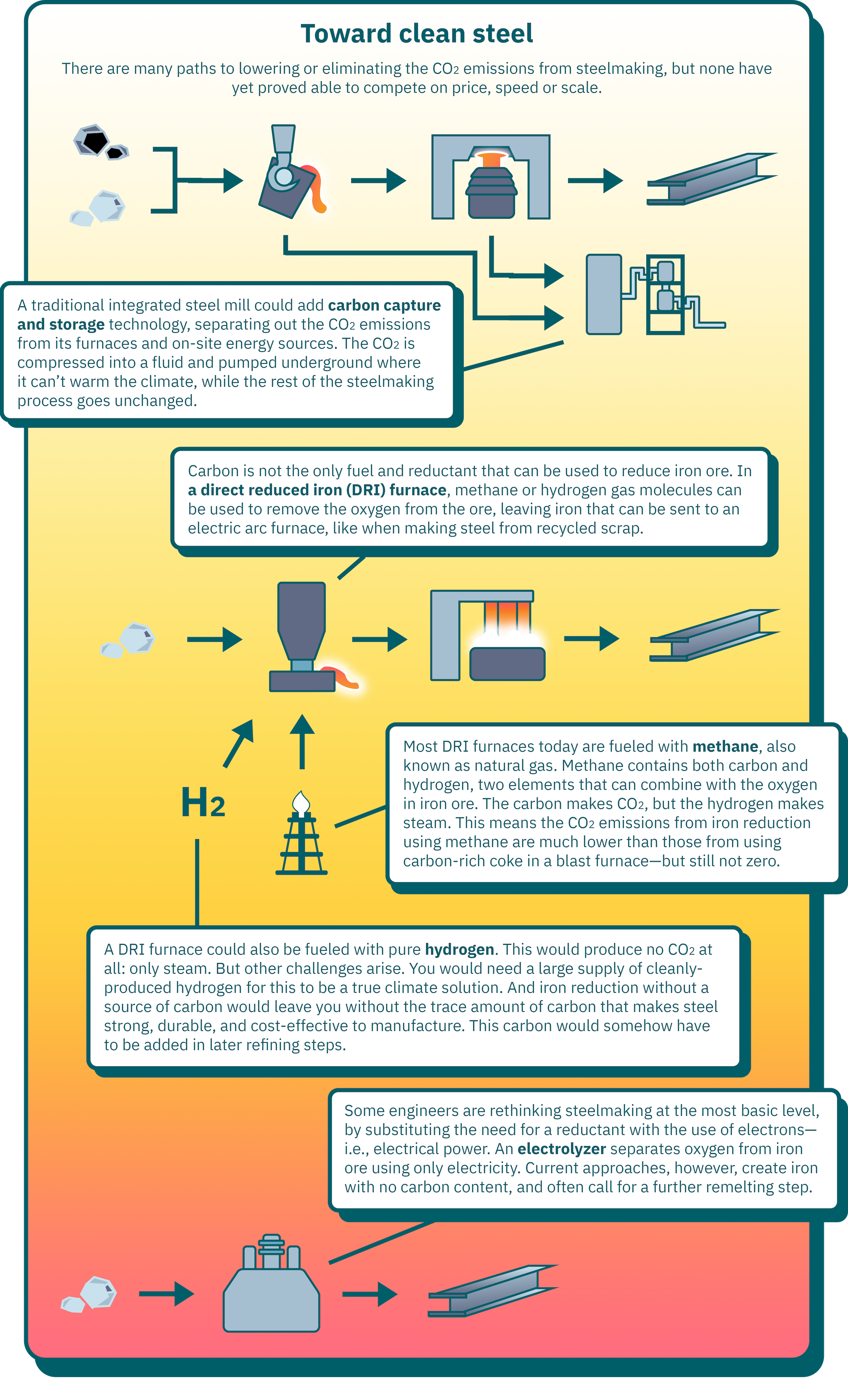
Click here to see information from the infographic above in a table.
Clean Steel Technology | Description | Challenges |
---|---|---|
Carbon capture and storage | A traditional integrated steel mill could add carbon capture and storage technology, separating out the CO2 emissions from its furnaces and on-site energy sources. The CO2 is compressed into a fluid and pumped underground where it can’t warm the climate, while the rest of the steelmaking process goes unchanged. | Carbon capture is a major additional cost, and requires a well-developed network of pipelines and storage sites to safely store the CO2 underground. |
Direct reduced iron furnace | Carbon is not the only fuel and reductant that can be used to reduce iron ore. In a direct reduced iron (DRI) furnace, methane or hydrogen gas molecules can be used to remove the oxygen from the ore, leaving iron that can be sent to an electric arc furnace, like when making steel from recycled scrap. | Depends on the fuel used. |
Methane | Most DRI furnaces today are fueled with methane, also known as natural gas. Methane contains both carbon and hydrogen, two elements that can combine with the oxygen in iron ore. The carbon makes CO2, but the hydrogen makes steam. This means the CO2 emissions from iron reduction using methane are much lower than those from using carbon-rich coke in a blast furnace. | DRI furnaces using methane are already commercially competitive. But while they have lower emissions than a blast furnace, the presence of carbon in the methane means that this inherently cannot be a zero-emissions process. |
Hydrogen | A DRI furnace could also be fueled with pure hydrogen. This would produce no CO2 at all: only steam. | Hydrogen is only as clean as its production process: you would need a large supply of cleanly-produced hydrogen for this to be a true climate solution. And the product is iron without the trace amount of carbon that makes steel strong, durable, and cost-effective to manufacture. This carbon somehow has to be added in later refining steps. |
Electrolyzer | Some engineers are rethinking steelmaking at the most basic level, by substituting the need for a reductant with the use of electrons—i.e., electrical power. An electrolyzer separates oxygen from iron ore using only electricity. | As with a hydrogen-powered DRI furnace, current approaches to electrolyzers create iron with no carbon content. They also often call for a further remelting step. |
Published June 28, 2024
1 World Steel Association: World Steel in Figures 2023.
2 International Energy Agency: “Iron and Steel Technology Roadmap,” October 2020. This report estimates that the iron and steel sector directly emitted 2.6 gigatons of CO2 in 2019, with an addition 1.1 gigatons of CO2 emissions from power consumption and the combustion of steel off-gases. The International Energy Agency reports this as 10% of global “energy system CO2 emissions,” but comparison with global emissions figures of all kinds, including from deforestation and other human land use, reduces this to 8.8%. (Global emissions figures taken from the same source and year as used in the IEA report for comparability: Friedlingstein, Pierre, et al., "Global Carbon Budget 2020." Earth System Science Data, Volume 12, Issue 4, 2020, doi:10.5194/essd-12-3269-2020.)
3 World Steel Association: Fact sheet: Energy use in the steel industry, April 2021.
4 RMI: “Forging a Clean Steel Economy in the United States,” Chathurika Gamage, Kaitlyn Ramirez, Nick Yavorsky and Lachlan Wright, March 9, 2023.